
在当今的制造业领域,企业往往只关注于表面的成本削减,如原材料和人工等显性成本,却忽视了隐藏在水面下的巨大隐性浪费。
数据冲击显示,全球制造业中有效增值时间仅占据生产周期的很少一部分,大部分时间都浪费在等待、搬运、返工等非增值活动中。
典型案例中,某家电企业年营收虽高达50亿,但经过精益诊断后发现,仅库存积压和过度生产两项,就每年吞噬了超过1.2亿的利润。
传统生产模式
思维逻辑是基于推动式生产(Push System),即“先生产再销售”的逻辑。
核心特征
采用大规模批量生产,追求设备利用率的最大化。
各部门间各自为政,导致信息流断裂。
依赖经验进行管理,问题解决存在滞后性。
相较之下,精益生产模式
思维逻辑则是基于拉动式生产(Pull System),即“只生产客户需要的”的理念。
核心特征
小批量流动,按节拍时间(Takt Time)精准匹配需求。
全流程价值流透明化,实现端到端的协同。
全员参与持续改善(Kaizen),追求不断进步。
传统痛点一:某机械厂仓库堆满长达6个月用量的螺栓,占用了高达800万的资金。
精益解法一:实施供应商协同的JIT(Just In Time)系统,并建立超市拉动系统(Kanban),以此提升库存周转率。
量化成果一:平均库存占用减少45%,释放了每年2600万的现金流。
面对传统生产模式下的种种弊端,国内领先的卫浴五金制造商正在进行精益转型。
改造前,车间的在制品堆积高达15天的用量,月度客户投诉超过300起,综合毛利率远低于行业平均水平。通过实施精益转型路径,包括价值流分析、快速换模(ED)以及拉动系统建设等措施后,企业取得了显著的成果。
精益生产的本质并非是“压榨式降本”,而是通过消除浪费、加速价值流动、赋能员工等方式,构建持续的竞争优势。相较于传统企业为数个百分点成本削减所付出的努力,精益先锋企业已经通过系统性的革新实现了更高幅度的成本重构。
在精益转型的过程中,企业需避免几个常见误区。不应只重视工具而忽视了文化的培养。不应盲目追求自动化而忽视了流程的简化。企业需要意识到,与供应链的协同是保证效率的关键,因此需要与关键供应商分享精益理念。
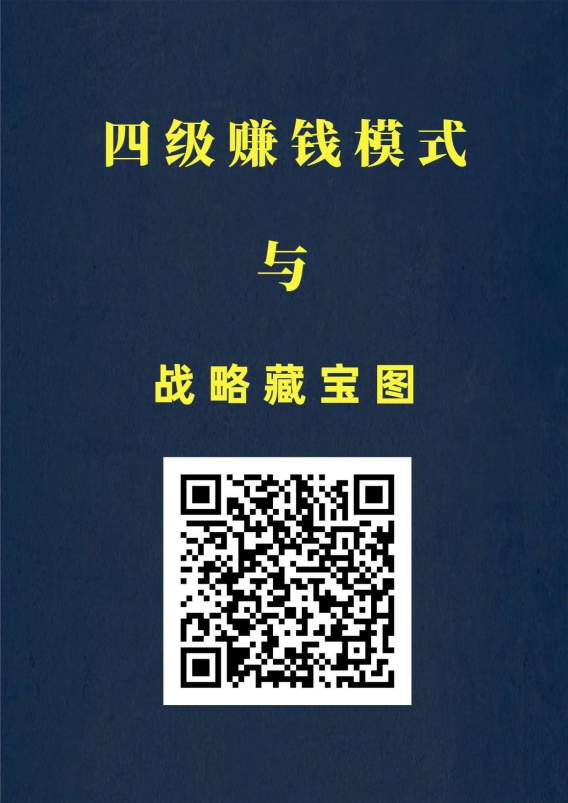